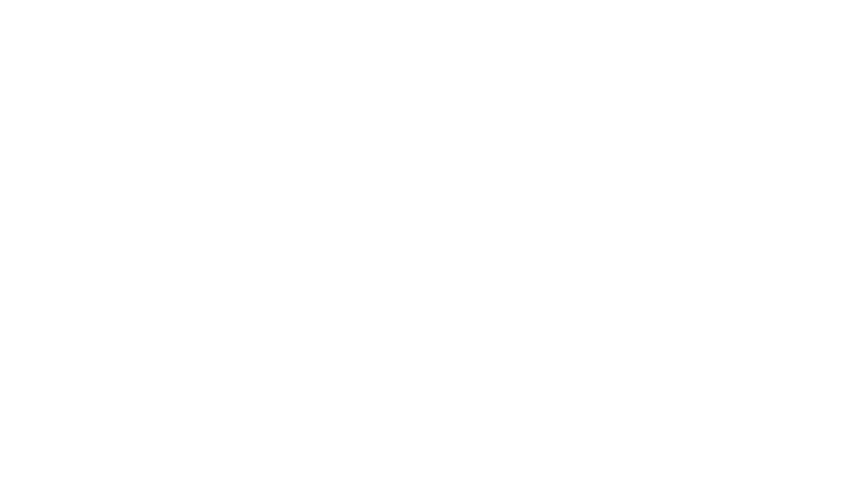
Dow is the second-largest global polyethylene (PE) producer, with a capacity of almost 10 million mt/year, as noted by Platts petrochemical analytics. The company’s productions and solutions are integrated across an array of sectors, including food packaging, furniture, crops and more.
Plastics remain a contentious issue on the sustainability spectrum. The material has been demonised, in large due to a lack of collection and a focus on single-use production that in turn has plagued the oceans. However, plastics, when used correctly, do serve a valuable purpose in the transportation and protection of goods amongst other key services.
Dow, like many major producers and users of plastics has introduced ambitious targets to try and improve the circularity of this material. Dow intends to enable one million metric tons of plastic to be collected, reused or recycled through its direct actions and partnerships by 2030.
The company also aims to close the loop by enabling 100% of Dow products sold into packaging applications to be reusable or recyclable by 2035.
How a business chooses to go about its phase-out of single-use, virgin and fossil-based plastics varies widely. Some are turning to alternative materials like metals, paper and bioplastics, while others are turning to reuse models and incorporating recycled plastics into new packaging and products.
For Dow’s packaging EMEA marketing director Romain Cazenave, the company is willing to be “selective” on how it phases out fossil-derived plastics, but is adamant that circularity has to be the main priority is Dow is to reach its sustainability and carbon goals.
“Plastics can still provide a service, but it comes down to which function you want to achieve,” Cazenave tells edie. “We want to provide the right service with a much lower carbon and material intensity. We are totally willing to be selective, and we look at the lifecycle analysis to see where plastics can be an efficient material.
“For me, there is room for growth in the usage of plastics because of its efficiency, but this is provided we become more circular and reduce the carbon intensity of our products. We need to be clear that whatever material reaches its end of life, it finds the right treatment, which is why circularity and recycling is the main focus.”
Bio-based approach
Big brands and retailers often criticised for their plastic packaging use are on course to reduce their virgin plastic use by one-fifth by 2025, according to a major report from the Ellen MacArthur Foundation.
According to the report, the virgin plastic use of all participating businesses peaked last year. In 2025, the cohort will use 20% less virgin plastic than in 2018, provided that they deliver on their commitments.
While Commitment signatories are on track to avoid the production of eight million tonnes of virgin, fossil-based plastics by 2025, the Foundation is urging brands to go further on using less plastics altogether. Recycled plastic is not automatically recyclable and, moreover, plastic cannot be recycled infinitely using technologies that exist at scale today.
A particular concern is now expressed about the lack of at-scale uptake of reuse and refill models. Only 5% of the brands participating are currently using refill or return models in some capacity. In comparison, 39% of signatories reported that they are substituting virgin plastic for recycled plastic in some cases, with that proportion rising to 41% for substitution with paper-based alternatives.
Dow, like many other firms, does incorporate bio-based feedstocks into its materials production. The company measures how much bio-based feedstock goes into its supply so it can measure how much can be sold as bio-based, through a term called a “mass balance approach”.
Indeed, the company notes that it is “poised to increase the percentage of bio-based feedstock going into our production lines”.
Most bioplastics produced globally come from carbohydrate-rich plants, such as corn or sugar cane, while second-generation bioplastics are produced from feedstock that doesn’t clash with food production, such as wood cellulose and short-rotation crops and waste materials like food waste and sawdust.
Dow’s sustainability policy and advocacy strategy director Carolina Gregorio claims that the company will produce bio-based plastics, but will not compete with other markets such as food production. One of the main challenges facing organisations turning to nature as a feedstock, either as products or fuel, is that the planet does simply not have enough land to account for production, food growth and – increasingly – carbon offsetting. Indeed, Oxfam estimates the land needed for current carbon removal plans issued by businesses could be five times the size of India, which is more than all of the farmland on Earth.
“We see that bio-based feedstocks will play a role, but with some clarification on what role they should play,” Gregorio says. “We want to utilise only biomass feedstocks that are coming from waste or by-products of other industries. We’re not going to compete with the food industry, it’s one of the conditions we’re defining when we say we want sustainable sources of biomass.
“This approach, whereby we preferentially use by-products for bioplastics will ensure that the carbon associated with those materials can be locked into the cycle as a material, rather than burnt as fuel. So we’re looking at bioplastics from the perspective of making the carbon more locked in and circular and ensuring they’re coming from those waste markets.”
Currently, the land use for bioplastics is only around 0.7 million hectares, equitable to 0.015% of global land area, and is set to increase to 0.020% of global land area in 2025. However, as land becomes more degraded and the demand for bio-materials continues to grow, businesses need to consider these wider implications, and the rising costs that will be incurred as demand shoots up.
Dow also reiterates that circularity is key, keeping products and therefore carbon in the loop for longer. While many businesses are exploring biodegradable or even the much more controversial oxo-degradable plastics, Cazenave notes that Dow does not want to generate any unintended consequences with its products.
Many bioplastics are biodegradable by nature, but usually only under high-temperature, industrial composting facilities. As a result, bioplastics can often end up in landfills, where greenhouse gas emissions are released upon breakdown.
Additionally, bioplastics and contaminate collected and recycled plastics, meaning that entire collections of plastics could be rejected from collection and sorting streams and end up in landfill.
“Biodegradable should be only used when the value chain needs it,” Cazenave says. “There is science and perception that it could be perceived as a good idea, but the application needs to be right. It’s not suitable for things like crisp packets, and it is not collected correctly then biodegradable becomes a nightmare, and impacts the quality of the system.
“It needs to be managed well and separated from other waste streams. The system needs to clearly identify the solutions for the consumer. Humans are not the perfect sorting machines, but biodegradable cannot end up in nature or other waste streams because the conditions won’t be right and the material will just fragment into microplastics. That is something we don’t want.”
Legislative engagement
Legislation will help with this and Gregorio notes that Dow has engaged with the EU on the revised Waste Framework Directive, which will allow biodegradable and compostable packaging to be collected together and used for anaerobic digestion. This is set to become mandatory throughout Europe by 2023.
Indeed, Dow continues to engage with policymakers on a global level to help with the transition to circular materials.
Gregorio claims that Dow welcomed the UN’s Plastic Treaty, likened as a Paris Agreement for plastics, which was introduced earlier this year. Nations agreed on a text which covers the full lifecycle of plastic, from production to waste management. It also covers plastics of all types and sizes, from large pieces of abandoned fishing gear, to nurdles and microplastics.
However, The American Chemistry Council industry group, which represents more than 190 member businesses including Dow, reportedly pushed back against the inclusion of measures to reduce plastic production globally.
Nonetheless, Gregorio welcomes the chance that the Treaty brings to work with different stakeholders to help improve the circularity of production.
“We immediately welcomed the resolution because of how it can globally drive the change that the plastics industry needs,” she adds. “We are going into our net-zero roadmap, so this is a tremendous opportunity. We like that in the discussions there are a lot of NGOs engaged with industry and governments and we feel this will be good to advance some harmonised measures across the board, especially in developing countries which are lacking waste infrastructure.
“It cannot be the case that waste is not managed, so if we can help improve the collection and sorting methods through a global movement, then this is good. So out first step is to make our products more recyclable and the second step is to work with industry to help improve waste collection to enable our circular transformation.”
While the need for recyclability alongside a dramatic uptake in reusables continues, Dow is moving ahead with short-term measures to drive circularity.
Dow recently announced a new collaboration with Mura, for example, on a new advanced recycling processes site in Germany. These new processes are expected to save approximately 1.5 tons of carbon dioxide per ton of plastic recycled, compared to incineration and reducing reliance on fossil-based feedstock, namely by reducing the amount of fossil-based feedstocks being used at facilities.
The Böhlen facility in Germany is expected to be operational by 2025 and when combined with other planned units would collectively add as much as 600KTA of advanced recycling capacity by 2030 for Dow globally.
The company believes that net-zero cannot be achieved without the circular economy and a big part of its decarbonisation plans relies on transitioning to both circular products and feedstocks.
The company’s Packaging and specialty sustainability director Peter Sandkuehler summarises the firm’s approach to driving circularity, noting that they’re “open to any solutions”.
“The Mura announcement is our first stepping stone,” he says. “But we have other partnerships in the pipeline which we aren’t ready to talk publicly about yet which will help take our circular goals to scale.
“There are different stages of our circularity aims to replace fossil feedstocks, but they’ll depend on regulations and the pricing of markets. For us, circularity is key and will probably grow more for us than bio-based uses, but we’re open to any solutions to help us move away from the fossil feedstocks and drive circularity.”
© Faversham House Ltd 2023 edie news articles may be copied or forwarded for individual use only. No other reproduction or distribution is permitted without prior written consent.
Please login or Register to leave a comment.