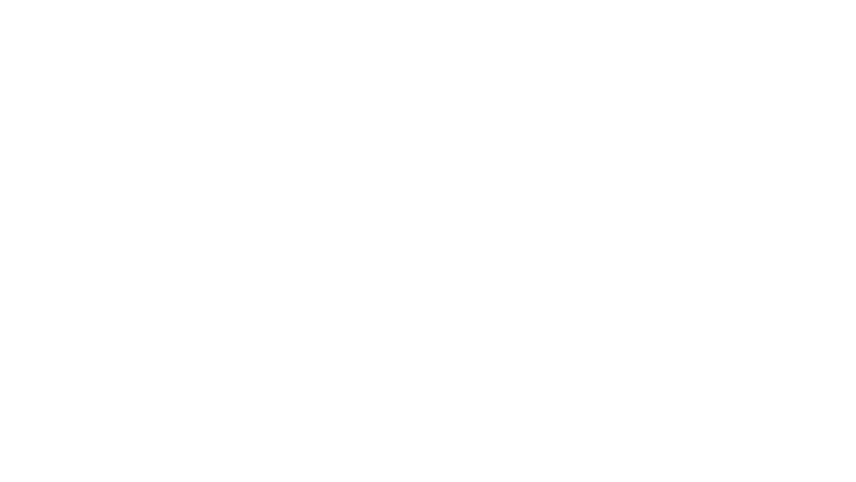
Dow is one of the largest materials science and chemicals firms in the world. Even if you haven’t heard of them, you will have interacted with their productions and solutions, which are integrated across an array of sectors, including food packaging, furniture, crops and more.
“Our products are everywhere,” Dow’s EMEAI Operations Vice president Kepa Diaz de Mendibil says, as he explains the company’s new three-phase plan to decarbonise its largest European site.
Consisting of 16 factories, a 90MW combined heat and power plant, 3,550 employees, and Dow’s international Research & Development Center, the Terneuzen site is the company’s second-largest globally and is a carbon-intensive, industrial behemoth.
It is also acting as the test bed for Dow’s decarbonisation plans, which include an ambition to reach carbon neutrality by 2050.
The company announced last year that it plans to reduce the site’s overall carbon emissions by 40% by 2030, and then aim for that carbon-neutral ambition by 2050.
Dow has split this plan into three phases that will require a massive amount of trust in innovation and low-carbon development, namely in the areas of hydrogen and carbon capture and storage (CCS).
Phase one
Dow plans to implement some short-term changes to the Terneuzen site in order to transform the by-products from core production processes, namely off-gas, and convert it into hydrogen and captured CO2. The hydrogen will be used as a “circular” fuel in the production process and Dow estimates that by creating a hydrogen plant onsite, they will be able to reduce emissions by approximately 1.4 million metric tons per year – equivalent to taking more than 300,000 cars off the road for a year.
The new hydrogen plant is expected to create around 3,500 construction jobs over a three-year period, followed by up to 500 permanent jobs at the site.
Diaz de Mendibil explains that the CO2 at the site would be captured and stored until Dow is able to introduce the latter phases and technologies of the three-point plan. The main aim is to utilise CO2 as a feedstock for production, rather than just storing it.
“We call our hydrogen clean or circular, because we don’t need to import it,” de Mendibil says. “We need to take our off gas, capture the CO2 and convert it into hydrogen. We aren’t importing natural gas, so we don’t class it as blue, we’re producing with what we already have here.”
Phase one of the plan would essentially enable Dow to transition from the use of grey to blue hydrogen while massively slashing emissions at the site.
Phase Two
The second phase of Dow’s plan brings the site close to the 2030 deadline for the 40% reduction. It would see CO2 captured from Dow’s ethylene oxide plant while also replacing several gas turbines with electrical alternatives in a move that would avoid an additional 300,000 metric tonnes of carbon emissions annually, bringing total annual reductions to 1.7m metric tonnes.
Indeed, the site is located next to a combined heat and power plant in Zeeuws-Vlaanderen near Terneuzen. The Electricity and Steam Association (ELSTA) plant generates energy in the form of heat and electricity for Dow’s complex and electrical power for supply to the national grid.
The heart of the plant consists of three gas turbines with a waste gas boiler and a steam turbine. The gas turbines can supply a maximum of 123 MW of electrical power. The steam turbine can supply a maximum of 90 MW of electrical power.
For Dow, the second phase of the plan will run until technological developments are made in the form of electrification, but will see them start to look at how the hydrogen produced at the site can go from being stored, to utilised.
“Generation two goes until we develop the technology for e-cracking and its industrial applications and until we have enough green power from the grid,” de Mendibil says. “Then we can build new furnaces at which point we don’t need the clean hydrogen, but we’ll still generate the off-gas, which we need to do something with.
“We will get this clean hydrogen across a range of applications, and the CO2 we’re extracting will go into chemicals. In a perfect world, by 2040, the CO2 will go to chemicals, the feedstock will be circular and we will not generate emissions.”
Phase Three
Phase Three is where Dow will have to explore unprecedented levels of innovation. The official line from the company is that it will aim to “develop and implement additional breakthrough technologies”.
An example is Dow’s previously announced collaboration with Shell to electrify ethylene steam cracking furnaces, called e-cracking. These furnaces currently rely on fuel combustion, which makes them CO2-emission intensive when not fired on clean hydrogen. Switching to electrical cracking with clean electricity will reduce the CO2 footprint of the production process to near zero emissions.
“We have to consider the technological readiness level of e-cracking,” de Mendibil adds. “In order to fire hydrogen in our furnaces and boilers, there is no technology risk and the capture of CO2 is also an existing technology, albeit one that needs more scaling. The beauty of generations 1 and 2, is that with a combination of existing technologies, there is no risk.
“E-cracking has more of a risk, it has not been implemented at an industrial level. We need to solve the technology challenge of e-cracking but from the sourcing of green power.”
Onsite solutions aren’t particularly viable for Dow due to the size of the plant in comparison to the ability to add solar capacity. However, In 2021, the company did add more than 900MW of renewable access globally and more than 25% of purchased electricity now comes from renewables.
In order, for e-cracking to be considered green, it needs to be powered by renewables and Dow believes that market shifts driven by high-level policy announcements should be able to complement this vision.
On 11 February 2022, the Dutch Government raised the offshore wind energy target from 11.5GW to about 21GW by 2030, which accounts for 16% of the nation’s energy requirements. Future scenarios for energy systems (and the North Sea Energy Outlook indicate that between 38 and 72 GW of offshore wind capacity will be required by 2050.
Due to the intermittent nature of renewables, a greener grid does not directly equate to green electricity at a given time. To this end, Dow and Diaz de Mendibil note that storage options could well be required, with the role of hydrogen again raised as one potential solution to this issue.
“In our third generation plan our electrical cracking will be done with electricity from the network, the key is that the electricity from the network needs to be green,” he says. “There’s no point in developing e-cracking if you don’t have green power in the grid.
“It is one thing having a lot of clean generation and we’re collaborating with authorities to look at energy storage capabilities, and one of those solutions could be hydrogen or ammonia generation.”
These “next generation” manufacturing technologies, including fluidized catalytic dehydrogenation (FCDh), ethane dehydrogenation (EDH) and electric cracking technology (e-cracking), are all at various stages on the development cycle, but given the current energy crisis, the Dow team note that they aren’t waiting around for long-term solutions to present themselves.
The long-term 2050 vision is accompanied by a shorter-term goal to reduce its net annual carbon emissions by five million metric tons versus its 2020 baseline – equitable to a 15% reduction.
Indeed, the company’s total carbon emissions have been reduced by 30% since 2005 while capacity has expanded globally.
The hard yards of this plan likely kick in beyond 2040, when the viability of e-cracking at an industrial scale will be put into action, as the company continues to decarbonise its sites, the role of hydrogen and CCS – two established yet contentious technologies that aren’t always considered green or cost effective – will be crucial to early success and Dow remains confident it can be done in harmony with renewables and closed-loop processes.
Indeed, short-term plans do exist, namely around the financial framing of new solutions, as well as continuing to close the loop on its products, which in turn helps lower emissions.
Dow recently announced a new collaboration with Mura, for example, on a new advanced recycling processes site in Germany. These new processes are expected to save approximately 1.5 tons of carbon dioxide per ton of plastic recycled, compared to incineration and reducing reliance on fossil-based feedstock, namely by reducing the amount of fossil-based feedstocks being used at facilities.
The company believes that net-zero cannot be achieved without the circular economy and a big part of its decarbonisation plans relies on transitioning to both circular products and feedstocks.
Be sure to check out edie’s follow up piece focused on Dow’s approach to the circular economy.
© Faversham House Ltd 2023 edie news articles may be copied or forwarded for individual use only. No other reproduction or distribution is permitted without prior written consent.
Please login or Register to leave a comment.